xEV용 배터리의 성능을 더욱 향상시키기 위해 용접부의 품질에 착목
초-저저항을 빠르고 정확하게 측정하여 품질을 향상
도입한 고객 소개
J사는 아시아 시장을 중심으로 전세계로 시장을 확대해 나가고 있는 자동차 제조사입니다. 이 회사는 초기단계부터 하이브리드 자동차(HEV)를 개발하고 판매해왔습니다. 최근에는 전동화로 이행하려는 글로벌 움직임에 맞춰 전기자동차(EV) 개발에도 주력하고 있습니다.
배경
배터리 용접부분의 품질을 더 빠른 단계에서 비파괴로 정확하게 판단하고 싶다
전세계적으로 SDGs 달성을 향한 의식이 고양되는 가운데, 많은 국가와 기업들이 ‘탄소중립, 탈탄소사회’를 실현하기 위한 활동을 추진하고 있습니다. 그 중에는 재생 가능 에너지나 전기자동차 이용이 예상되고 있어, 앞으로 더욱더 활용이 기대되는 것이 축전지입니다. 특히 리튬이온배터리는 전기자동차(EV)보급과 함께 크게 수요가 늘어날 것으로 여겨지고 있습니다.
고전력화, 대형화, 대폭적인 비용 절감이 기대되는 가운데, 긴 수명에 안정성이 높은 리튬이온배터리에 대한 수요는 높아지고 있습니다. 다양한 응용분야로 확대되면서 배터리에 더 높은 성능이 요구되고 있습니다.
세계 시장을 겨냥한 EV개발에 주력하고 있는 자동차 제조사 J사에서도, EV에 탑재하는 리튬이온배터리의 성능 향상을 위해 오랜 시간을 개발해왔습니다. 예측되는 여러 요소들을 반복해서 개량해 배터리 성능을 향상시켜온 J사가 최근 주목하고 있는 것이 배터리의 용접부분의 품질 향상입니다. 배터리셀과 배터리팩을 제조하는 과정의 여러 연결부분에서 용접이 실시됩니다. 특히 전기적 경로에 관한 용접 품질이 불량인 경우 배터리는 본래의 성능을 발휘하지 못합니다.
지금껏 J사에서는 용접기의 동작상황을 감시하거나 용접부분의 육안검사와 화상매칭검사를 이용해 불량품을 제거하고 있었습니다. 하지만 랜덤샘플검사에서 실제로 용접부분을 파괴해 확인해보니 양품이라 판정한 제품이 불량품이거나, 불량품으로 제외시켰던 제품 중에 양품이 섞여있거나 하여 양불판정의 신뢰성이 낮았습니다. 불량품 발견이 늦어져 후공정에 나가버리면 배터리의 제조비용에 크게 영향을 줍니다. 최악의 경우 불량품이 시장에 유출되고 맙니다. J사로서는 더 이른 단계에 파괴없이 정확하게 배터리의 품질을 판단할 수 있는 수단이 필요했습니다.
각형 모듈
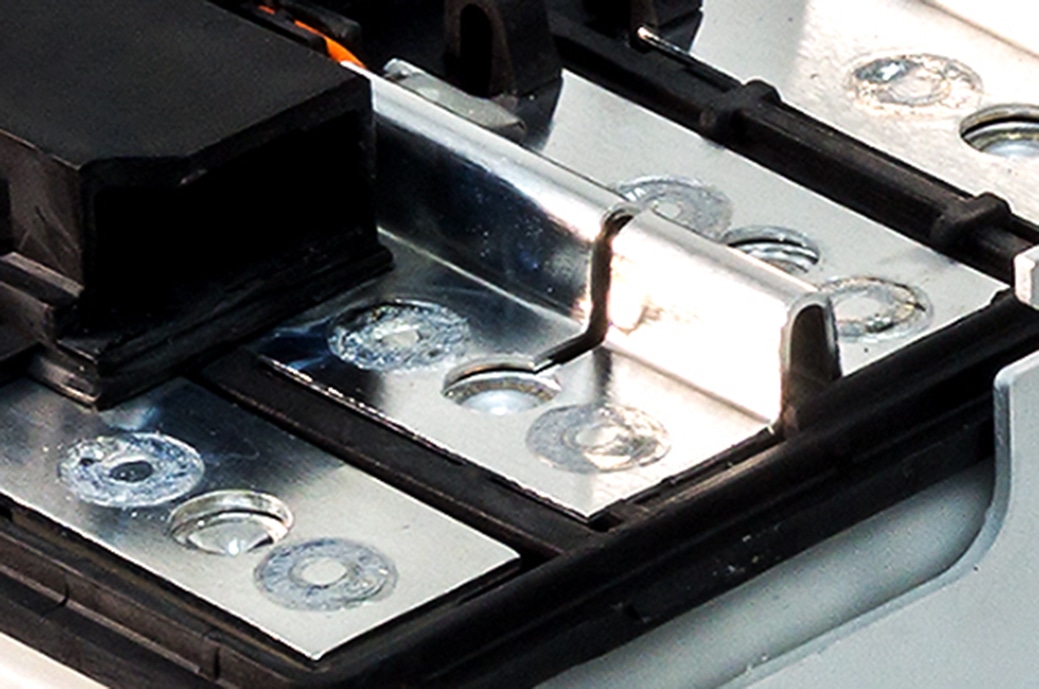
용접부
고객이 HIOKI 제품을 선정한 포인트
DMM으로는 감지하지 못하는 초-저저항을 빠르고 정확하게 측정할 수 있는 전용기를 높게 평가
용접의 보이지 않는 부분의 품질을 높은 재현성으로 수치화하기 위해 주목한 것이 기존의 품질 검사에 추가로 전기적 용접저항을 측정하는 것입니다. 저항값이 클 경우에는 리튬이온배터리의 충방전 시에 발열하는 원인이 되어 고온에 의한 성능 열화뿐만 아니라 화재로 이어질 위험도 있습니다. 배터리의 성능과 안전성이라는 2가지 측면에서 J사는 용접부분의 저항측정을 제조공정에 도입했습니다.
하지만 세계적으로 수요가 증가하고 있는 리튬이온배터리는 빠르게 대량생산이 요구되고 있어 저항측정에 걸리는 시간이 가능한 짧아야 합니다. 또한 소형화되어 가는 전자부품과 달리, 자동차용 차량배터리나 부스바 등은 대형화 일로를 걷고 있습니다. 그에 반비례하듯이 저항값은 작아지고 있습니다. 큰 측정대상에 대해 μΩ 단위의 매우 작은 저항을 정확하게 측정해야만 하여 그 난이도는 대단히 높아졌습니다.
J사에서는 당초 전압측정 공정에서 사용하던 디지털 멀티미터(DMM)를 사용해 용접저항도 계측하고 있었습니다. 하지만 DMM의 저항측정능력으로는 용접부분의 초-저저항을 정확하게 검출하지 못한다는 것을 깨닫고, 초-저저항 측정에 대응하는 전용 측정기를 도입할 것을 검토했습니다. 여러 제조사를 검토한 끝에 선택한 것이 HIOKI저항계 RM3545-02였습니다.
이 RM3545-02는 이제껏 수많은 저항계를 개발해오며 다양한 업계에서 이용 실적을 쌓아온 HIOKI가 전기적 저항을 정확하게 측정하는 노하우와 기술을 담은 제품입니다. 특히 초-저저항 계측에 강하여 0.01μΩ부터 1200MΩ까지 광범위하게 저항을 측정할 수 있는 점이 J사의 요구사항에 들어맞았습니다.
측정 예 : 저항계 RM3545-02
접촉부
또한, 배터리셀이 여럿 연결된 배터리팩에서는 큰 전압이 발생합니다. 배터리팩의 부스바 용접의 저항측정에서는 이 큰 전압 때문에 측정기기가 고장나기도 하여 양산라인의 다운타임을 초래하는 경우도 있습니다. J사는 이 과입력전압을 방지하는 역할을 하는 보호유닛을 함께 도입했습니다.
도입 후 효과
용접부분의 초-저저항 측정을 ‘신속・정확・안전하게’ 자동으로 실시
나아가 J사는 배터리팩의 부스바 용접 검사공정에 저항계 RM3545를 자동 검사 시스템 FA1240-60에 탑재한 자동 측정 시스템을 구축했습니다.
배터리팩의 부스바 용접 측정에서는 프로브에 의한 측정위치가 1mm어긋난 것만으로 수십μΩ이나 바뀌게 됩니다. 그만큼 위치의 정밀도가 중요한데 HIOKI의 우수한 프로빙 기술로, 신속 정확 안전하게 저항을 자동 측정할 수 있게 되었습니다.
다른 검사 공정에서는 배터리셀 내부의 전극시트와 탭 리드의 용접저항 측정시간을 단축하기 위해 고속 다채널화를 추진했습니다. RM3545-02에 슬롯 방식으로 내장하는 Z3003 모듈을 장착해 1대로 최대 20ch의 고속 전환이 가능해졌습니다. 덕분에 1개 트레이에서 반송되는 여러 제품을 한꺼번에 측정할 수 있게 되어 설비의 설치면적은 그대로인채, 저렴한 비용으로 생산라인 전체의 반송시간을 줄일 수 있게 되었습니다.
RM3545-02에 멀티플렉서 유닛 Z3003을 장착
Z3003을 2 유닛 실장 시 20곳을 다점 측정 (4단자 측정 시)
이 RM3545-02에 FA1240-60과 Z3003을 탑재한 자동 검사 시스템을 구축한 덕분에,이제껏 파괴시험으로밖에 파악할 수 없었던 용접부분의 품질을 정확하게 수치화할 수 있게 되었습니다. J사의 담당자는 이렇게 난제인 초-저저항 측정을 자동으로 빠르게 대량 실시할 수 있게 된 것이 EV에 탑재하는 리튬이온배터리의 성능과 품질 향상으로 이어졌다고 말합니다.
J사에서는 향후 주변기기로 스위칭 메인프레임 SW1002와 멀티플렉서 모듈 SW9001을 추가해 측정 채널 수를 최대 132ch까지 늘려 검사공정의 더 높은 고속화와 안정화를 도모할 것을 검토하고 있습니다.
-
스위치 메인프레임 SW1002와 BT356x시리즈 조합 예
그 외에도 최대 1000V 전압에 대응하는 BT356x 시리즈를 도입할 것을 검토하고 있습니다. 앞으로도 폭 넓은 선택지와 솔루션을 지닌 HIOKI의 협조를 얻어 리튬이온배터리의 성능 향상을 위해 연구 개발을 매진해 나갈 방침입니다.
도입한 제품
향후 도입 예정인 제품